AAMA 501.2 Test Explained And What You Need to Know
The AAMA 501.2 test is a crucial tool in the construction industry. Simply put, it’s a quality assurance measure designed to assess water penetration resistance in building envelopes, specifically newly installed fenestration products such as storefronts, curtain walls, and sloped glazing systems. But what does this mean for you? If you’re an architect, contractor, or property owner, this test is vital. It helps ensure the integrity of your building against water intrusion, preventing potential damage and costly repairs.
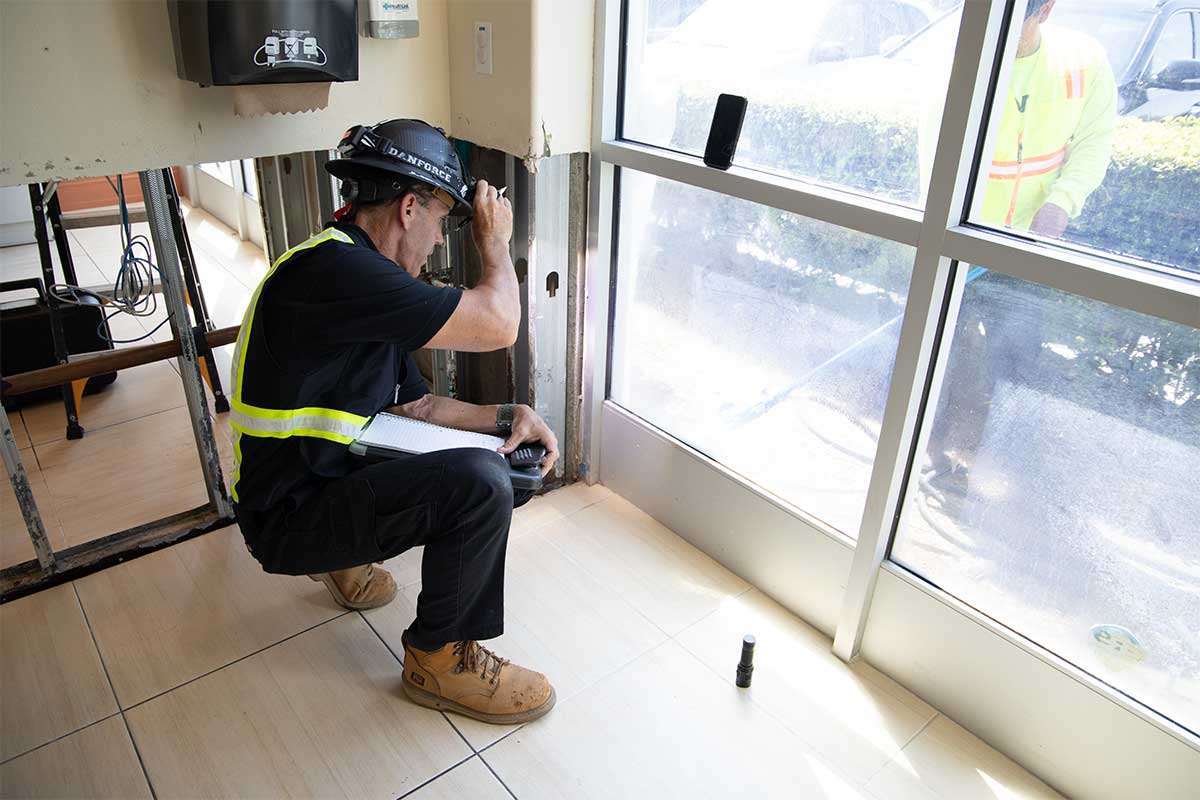
In states and cities like Las Vegas, Nevada, Los Angeles, California, and Phoenix, Arizona, the AAMA 501.2 test is extremely relevant. Interestingly enough, these regions have diverse climates, making the buildings located in these cities susceptible to varying weather conditions.
This article will provide a comprehensive guide to the AAMA 501.2 test. We’ll cover its procedures, benefits, and regional considerations. By the end, you’ll understand why this test is a key component in maintaining the health and longevity of your building.
Introduction to AAMA 501.2 The Scope and Purpose
Basically, the AAMA 501.2 test is an on-site evaluation method used to determine the water penetration resistance of installed windows, doors, and curtain walls. Designed by the AAMA (American Architectural Manufacturers Association), this test plays a key role in assuring quality and performance in construction. Administering the test procedure involves using a calibrated spray rack system to apply water to the exterior surface of the building’s window system. While the water is applied, the interior is inspected for any signs of leakage.
To clarify, this test is recognized for its non-destructive approach much like infrared thermography. It allows inspection without harming the structural integrity of the component being tested. Importantly, the AAMA 501.2 test helps identify potential leaks that could lead to water damage, mold growth, or even structural degradation. In essence, the AAMA 501.2 test serves as an important diagnostic tool. It helps building professionals ensure that the components can withstand the elements and function as intended.
AAMA STANDARD
What does the AAMA 501.2 standard say?1.1 The purpose of this document is to provide a quality assurance and diagnostic field water penetration check method for installed storefronts, curtain walls, and sloped glazing systems. The procedure outlined in this document is not intended to test the rated or
specified water performance representative of a wind-driven rain event. AAMA 503 is the proper test method for field testing of storefronts, curtain walls, and slope glazing for air leakage resistance and water penetration resistance performance.
NOTE 1: This field check method is not appropriate for testing operable components such as operable windows and doors. AAMA 502 is the proper test method for field air leakage resistance and water penetration resistance testing of newly installed operable windows and doors and AAMA 511 is the proper test method for forensic water penetration testing of fenestration products.
1.2 This field check procedure is intended to evaluate those joints, gaskets, and sealant details in the glazing that are designed to remain permanently closed and watertight.
1.3 The primary units of measure in this document are metric. The values stated in SI units are to be regarded as the standard. The values given in parentheses are for reference only.
1.4 This document was developed in an open and consensus process and is maintained by representative members of AAMA as advisory information.
Importance in Building Envelope Testing
Building envelope testing encompasses a variety of assessments aimed at ensuring the integrity of a building’s outer shell also known as the “envelope”. Among these, the AAMA 501.2 test stands out as one of the many tests like the ASTM E1105, for its focus on water penetration, a key area of concern for building durability. Water intrusion can compromise not just the aesthetics but the safety and energy efficiency of a building. Mold, rot, and structural weakening are some consequences that can occur if water penetration is not checked. The AAMA 501.2 test specifically addresses these risks by simulating rain conditions to test for leaks in any state we work in such as Arizona, California, and Nevada.
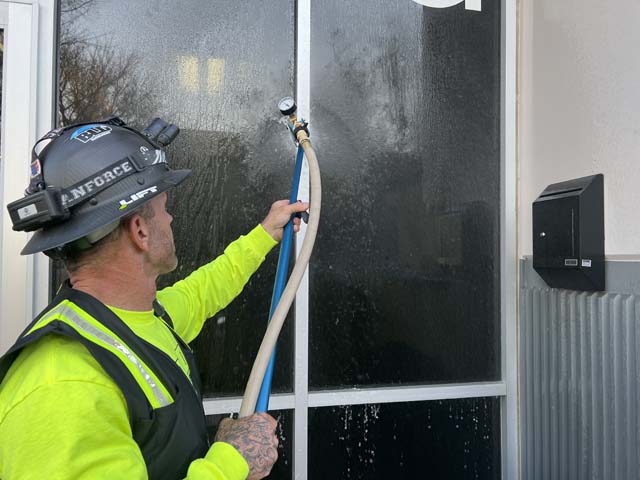
New or remodeled commercial buildings often require this test as part of their building standards or specifications. It is particularly crucial in environments with high rainfall or extreme weather, which can exacerbate water intrusion issues like Arizona, Nevada and California.
Incorporating AAMA 501.2 testing as part of the initial quality assurance test and then later into routine maintenance ensures that potential problems are detected early. This proactive approach extends the lifespan of the building and reduces repair costs, making it an essential part of building envelope management.
Overview of Building Leak Detection and the Types of Water Intrusion Testing
Water intrusion testing is crucial for identifying and addressing potential leaks within a building’s envelope. Various tests are available like the ASTM E1105, AAMA 547, ASTM 2128 etc…., each catering to different aspects of water leak detection. Understanding these individual test types helps in selecting the most suitable method for your specific needs.
One common type is the static water penetration test. This test simulates rainfall conditions on a component for an extended period usually 15-20 minutes. It is particularly useful for testing windows or doors and other exterior installations.
Another critical type is the dynamic water penetration test. This combines wind and water to replicate storm conditions, providing a more comprehensive evaluation. It is often used in combination with static testing for added assurance.
Another form, the ASTM 5957 flood test, is primarily used on flat decks. This involves temporarily flooding a section of the deck to observe water path behavior and spot vulnerabilities. Finally, infrared thermography offers a noninvasive way to detect moisture. This approach uses thermal imaging to identify cold spots where moisture might accumulate.
In summary, common water intrusion tests include:
- Static water penetration test
- Dynamic water penetration test
- Flood test
- Infrared thermography
- Each test has distinct uses, and choosing the right one depends on the building’s components and environmental conditions.
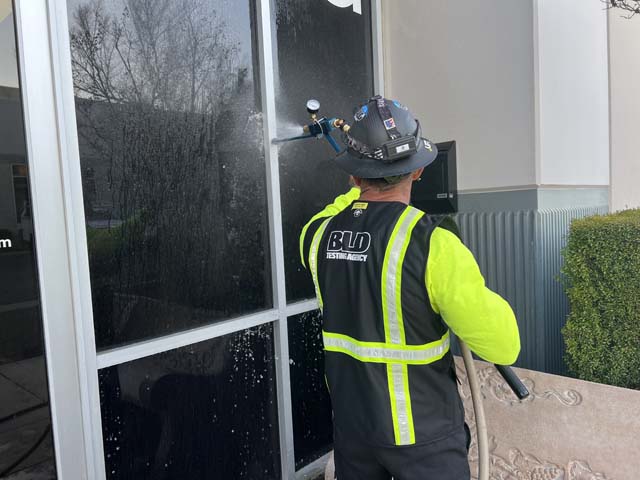
Preparation Of the AAMA 501.2 test Area
All the frames and/or units must be put in place on the building’s lowest two standard floors for testing the curtain wall and on the lowest standard floor for testing the storefront or sloped glazing system. The whole area must be covered with glass for the work to be finished. You must carefully follow the approved shop drawings and job specs when doing this work. An area of the finished part will be chosen by the architect and/or the owner’s representative to be tried.
The test area should be a good example of normal construction, and shouldn’t have any obvious flaws or items still on the “punch list.” If a test area and/or site has not been chosen, the people who are giving the test will choose one. This area, normally at least 9.3 m2 (100 ft2), will be chosen to provide accurate performance data. There should be border caulking, standard splices, frame intersections, and, if needed, at least two full vision lites and two full spandrel lites with an intermediate vertical member and an intermediate horizontal member in the area that needs to be tested. In the test area, all parts that can work must be separated and not put through the test process.
ASTM 501.2 Standard
What does the standard say?All of this work shall be done in strict accordance with approved shop drawings and job specifications. The architect and/or owner’s representative shall designate an area of the completed portion to be tested. The test area shall be a representative sample of typical construction and shall have no outstanding punch list items or other visible defects. If no test area and/or location has been identified, the persons doing the test shall select an area. This area shall be selected to provide representative performance data, usually a minimum of 9.3 m2 (100 ft2).
The area to be tested shall include perimeter caulking, typical splices, frame intersections, and, if applicable, at least two entire vision lites and two entire spandrel lites containing an intermediate vertical member and an intermediate horizontal member. All operable components within the test area shall be isolated and exempt from the test procedure.
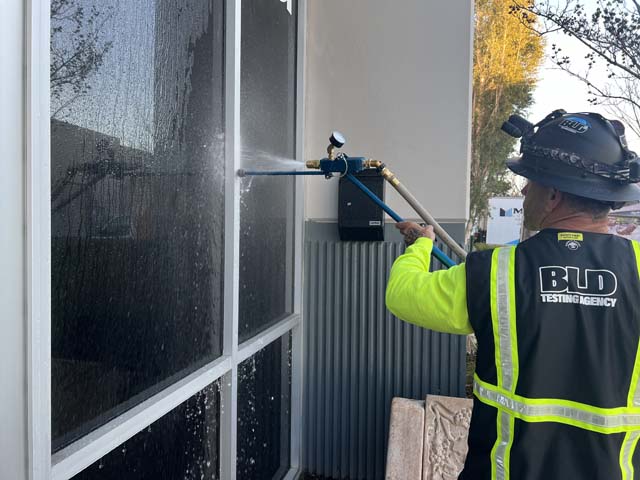
Common Methods and Techniques of the AAMA 501.2 Test
Different techniques are employed for building leak detection, depending on the specific environment and material. These methods can pinpoint the origin of water intrusion with precision, aiding in effective remediation. One basic technique is visual inspection. While it relies on the assessor’s expertise, it helps identify obvious signs of leakage such as water stains or mold growth.
For reference, prevalent leak detection methods include:
- Visual inspection
- Smoke testing
- Blower door testing
- Moisture meters
- Electronic leak detection
- Smoke testing serves as an alternative method. This involves using smoke to track air and water paths, highlighting less visible entry points.
- Blower door testing is also popular, focusing on air leakage as a potential pathway for water intrusion. This test uses a powerful fan to pressurize or depressurize a building and assess air leakage rates.
- Moisture meters can directly measure the moisture content within walls and floors. They are indispensable for pinpointing the exact areas that need repair.
- Electronic leak detection employs electric fields to trace moisture paths and provide a detailed map of leak locations, which is handy on roofs.
Together, these techniques provide a comprehensive toolkit for addressing building envelope vulnerabilities. Selecting the appropriate method depends on the specific challenge and building characteristics.
AAMA 501.2 Testing Procedures-Equipment and Set-Up
The AAMA 501.2 test requires specialized equipment to ensure accurate results. The primary tool is a calibrated spray rack system. This apparatus mimics rainfall by dispersing water evenly over the test area. Precise calibration is crucial to replicate natural rain conditions correctly. Pressure gauges are also essential. These devices measure the water pressure and ensure it remains consistent throughout the test. Maintaining accurate pressure prevents skewed results and ensures reliable assessments.
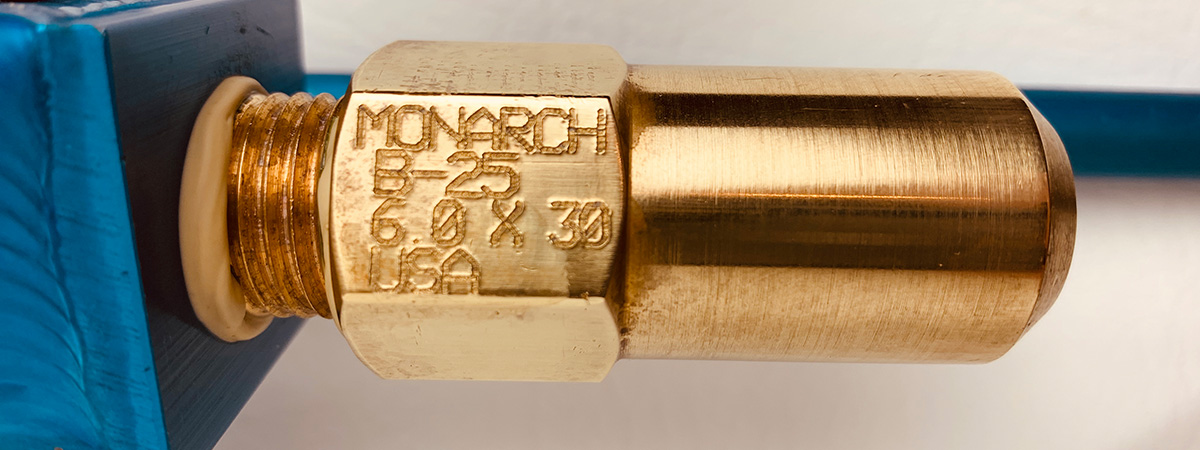
A control valve system is part of the setup. This system regulates water flow and pressure, allowing testers to adjust conditions as needed. Control valves help simulate different environmental situations effectively. The test area must be carefully prepped. This involves sealing the area to prevent extraneous water interference. Additionally, monitoring systems should be in place to observe any water penetration during the test.
It’s vital to have a qualified team conduct the setup. Certified professionals understand the intricacies of the equipment and can adjust settings for optimal accuracy. Proper setup ensures the integrity and validity of the test results.
Step-by-Step 501.2 Testing Process
Conducting the AAMA 501.2 test involves a systematic process. Each step must be executed with precision to ensure accurate detection of water intrusion points. Here’s a closer look at the procedure:
- First, assess the testing site conditions. Ensure the environment mimics realistic weather scenarios, aligning with local weather patterns.
- Second, set up the calibrated spray rack. This equipment should be positioned at the correct distance from the test surface, ensuring even water distribution.
- Third, initiate the water spray at the designated pressure. Use pressure gauges to measure and maintain this pressure throughout the test to mimic natural rain conditions.
- Fourth, continuously monitor the interior side of the test specimen for any signs of leakage. Observations during this phase are critical for identifying potential water intrusion points.
- Fifth, the testing duration generally lasts about 15 minutes. However, this time may vary based on specific building codes or testing requirements.
- Sixth, post-test inspection is necessary. Examine both the exterior and interior thoroughly to ensure all observations are documented.
- Finally, document the results for further analysis. Accurate records aid in addressing detected issues and are important for maintenance and future reference.
The testing process requires a high degree of expertise. Each step not only helps in pinpointing vulnerabilities but also aids in ensuring the building’s envelope integrity. Regular testing, as detailed above, plays a critical role in maintaining the longevity and safety of the structure. Following the process ensures consistent and reliable results, making the AAMA 501.2 test an essential tool in building envelope assessment.
Regional Considerations | Nevada AAMA 501.2 Testing
Nevada’s climate is primarily arid, but it occasionally experiences heavy rainfalls. Such weather conditions make AAMA 501.2 testing crucial. It ensures buildings withstand the sudden onslaught of water without compromising envelope integrity. Buildings in Nevada often face challenges due to rapid temperature changes. These fluctuations can cause materials to contract and expand, impacting sealants and joints. Regular 501.2 testing helps identify areas susceptible to water intrusion.
Testing in Nevada focuses on durability against both dry conditions and unexpected rains. It aids property owners in preventing costly water damage and maintaining structural safety. Ensuring buildings meet necessary water resistance standards through regular testing is vital for long-term resilience.
Arizona AAMA 501.2 Testing
Arizona is famous for its monsoon season, which brings intense rainfall over a short period. This makes 501.2 testing essential for buildings in the state. The test helps ensure structures can withstand these abrupt weather events without water intrusion. The desert climate creates unique challenges, with extreme temperature variations and strong winds. These factors can compromise building envelopes over time. AAMA 501.2 testing assists in identifying and addressing vulnerabilities that may not be apparent during dry months.
Regular testing in Arizona assesses the effectiveness of existing protective measures. It provides critical data to adjust maintenance plans and enhance the building’s resistance against aggressive weather patterns. Proactive testing keeps buildings in prime condition, safeguarding them against the elements.
AAMA 501.2 Testing in California
California’s diverse climate zones require adaptable building solutions. Coastal areas face moist, salty air, while inland regions deal with dry, hot weather. AAMA 501.2 testing helps manage these varying challenges by ensuring building envelopes can endure them all. Rainy seasons and sporadic storms also affect different regions across California. These conditions necessitate thorough testing to detect any potential weak points in a building’s defense against water intrusion. Failure to do so can lead to significant damage over time.
With California’s range of climatic environments, testing helps tailor solutions to specific regional needs. AAMA 501.2 tests inform maintenance and repair decisions, supporting long-term structural integrity. Regular testing is key to maintaining buildings resilient to California’s unique weather demands.
Conclusion | The Benefits of AAMA 501.2 Testing
The AAMA 501.2 test is a reliable way to ensure buildings remain water-tight and structurally sound. This test offers essential insights into the performance of building envelopes, providing an opportunity to address water intrusion risks. Regular testing prevents costly water damage and contributes to longer building life spans. By identifying potential issues early, property owners can make necessary repairs before minor leaks become major problems. This approach helps in maintaining property value and occupant safety.
Moreover, the test supports compliance with building codes and specifications, often a legal requirement. Although it is recognized industry-wide as a benchmark for quality assurance, instilling confidence in both builders and owners. This comprehensive approach solidifies the importance of the AAMA 501.2 test in building maintenance.
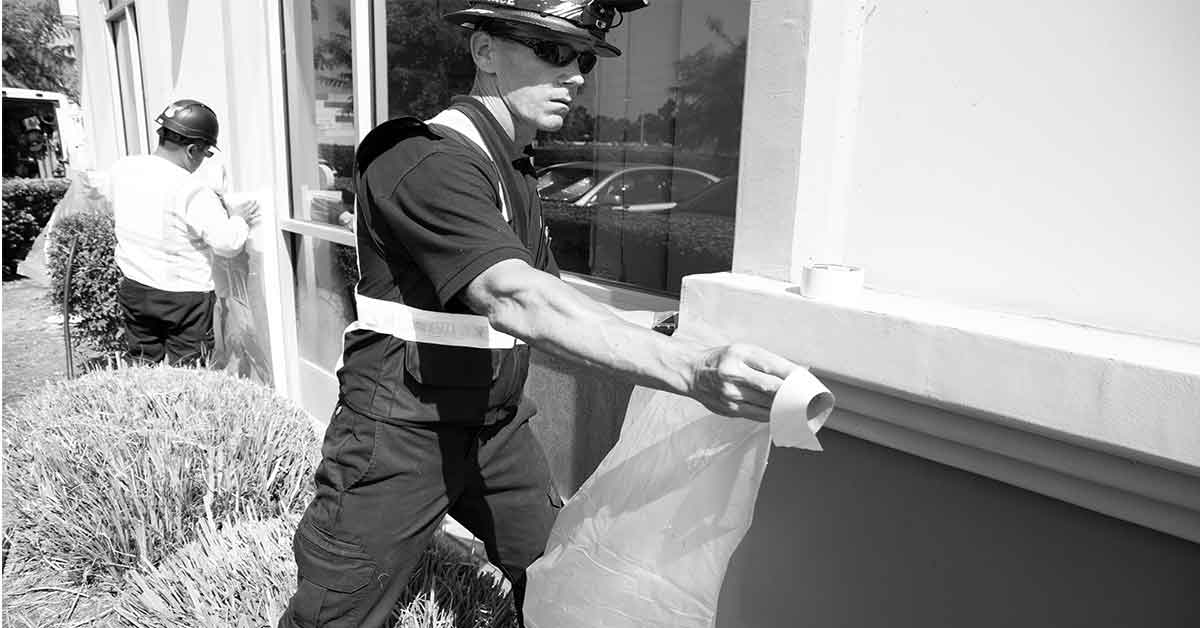
Future Trends in Water Intrusion Testing
As technology advances, water intrusion testing continues to evolve. More precise equipment and innovative testing techniques are emerging, enhancing accuracy and efficiency. These developments promise even more effective methods to detect water leaks. Sustainability and energy efficiency are growing priorities in construction. Future tests might integrate energy performance assessments, providing a more holistic analysis of building envelopes. Nevertheless, by merging with green building practices, the AAMA 501.2 test could further its relevance in eco-friendly construction.
Automation and remote monitoring are also potential trends in testing. They could offer real-time data analysis, allowing for proactive maintenance strategies. As these technologies become more widespread, they will likely shape how water intrusion tests, like the AAMA 501.2, contribute to building excellence.